Best Fuel Safety Practice
Mar 15, 2023
Article Provided by: Rick Limon
From checking spare parts inventory to squeezing in one more maintenance check, equipment is always top of mind as you prepare for a busy season. While it’s crucial to ensure engine compone
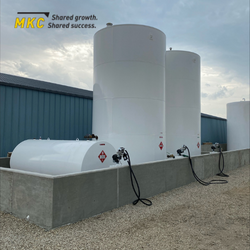
Two key things affect the quality of your fuel supply: keeping bulk fuel storage clean and choosing the right fuel.
Better bulk fuel storage
If there’s one thing that should be done during preparations, it’s cleaning contaminants and other debris that may have accumulated in the tank. That debris can be pumped into your equipment and cause engine build-up that leads to less-than-optimal performance and eventually can require expensive repairs. To reduce the risk, check fuel tanks for moisture at least once per year and service if needed. It's also important to switch out filters annually or sooner depending on volume.
Equally as important is getting rid of debris in your tank, is keeping moisture out of your fuel supply. Fuel contaminated with water can cause decreased acceleration, loss of horsepower and, in some cases, engine damage that spells costly downtime. Water in your fuel also allows for microbial growth to form inside your tank and attack your fuel. Large temperature swings from hot afternoons to cool mornings add to the risk with increased condensation.
You can do a few things to mitigate water accumulation in fuel tanks. The first is to utilize equipment drain valves. Drain valves will remove water from machinery and storage tanks, minimizing the impact that water will have on a busy season.
Another easy way to reduce water in equipment is to simply fill up the fuel tank at the end of each day. Condensation happens overnight, especially in the spring through early summer. Filling the tank will reduce airspace, thereby reducing the risk of water.
High-quality fuels deliver high-quality performance!
As technology evolves, ag equipment and diesel engines are becoming more advanced and now, more efficient Tier 3 and Tier 4 engines are expected to perform at high levels during the busiest seasons. These newer engines have tighter tolerances for imperfections like dust, rust and other corrosive materials, making it especially important to protect engine components.
A key way to maintain and get the most bang for your buck from your equipment is by investing in premium diesel fuel. When it comes to planting and harvest, time is of the essence. The savings and additional horsepower that can be gained with a premium diesel fuel will pay off in the long-run. CENEX® RUBY FIELDMASTER contains industry-leading additives to stand up to harsh conditions throughout planting, growing and harvest.
Now is also a great time to take a good look at your pumps, hoses, nozzles and filters. Any filters installed by MKC will have a date on them showing when they were installed. Our drivers and sales staff can help in getting those changed if needed.
In addition, now is the time to fix any leaks, broken equipment, or problems before the busy season. So, please look over these components and let us know how we can support you by calling your area energy consultant or by calling the energy office at 620-241-1885.